In the dynamic world of display technology, understanding the subtleties of components like LCD glass is crucial. This tiny yet significant element plays a pivotal role in the functionality and durability of LCD displays. As technology evolves and consumer demands shift, the characteristics of LCD glass, especially its thickness, have become a focal point for manufacturers and tech enthusiasts alike.
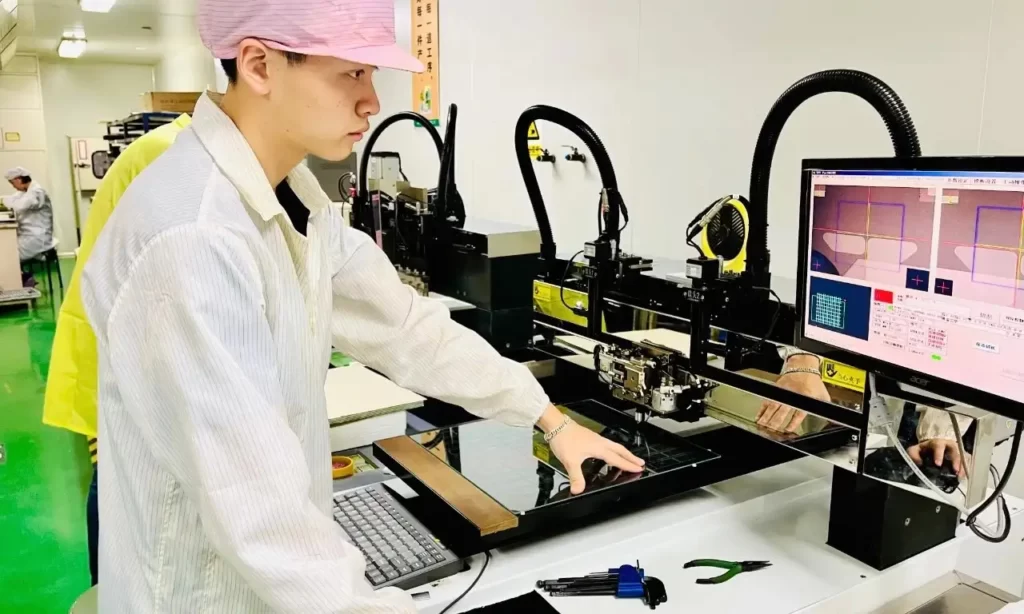
LCD glass thickness varies depending on the type and use of the display, typically ranging from about 0.3mm to 3mm. This variation is essential for balancing display clarity, durability, and manufacturing costs.
This blog post delves deep into the intricacies of LCD glass, exploring what it is, why its thickness matters, and the factors influencing its dimensions. Whether you’re a tech aficionado or a professional in the display industry, understanding these aspects is key to appreciating and making informed decisions about LCD technology.
Understanding LCD Glass
What is LCD Glass?
LCD (Liquid Crystal Display) glass forms the core of LCD technology, housing the liquid crystals that enable image display. This transparent layer is not just a protective covering; it’s integral to controlling the display of images on the screen. The unique properties of LCD glass, such as its transparency and ability to conduct electricity, make it an indispensable component of LCD screens.

The Role of LCD Glass in Display Technology
LCD glass doesn’t just protect the delicate internal components; it actively participates in the display process. The alignment of liquid crystals and their manipulation by electrical currents happen within this glass layer. This manipulation is what creates the vivid images we see on screens. LCD glass must maintain a delicate balance: it should be thick enough to protect and support the internal components but thin enough to allow precise control of the liquid crystals.
Learn more about How to Make LCD Glass?
Factors Influencing LCD Glass Thickness
Size and Application
The thickness of LCD glass largely depends on the size of the display and its intended application. Larger displays, like those used in TVs and monitors, generally require thicker glass for added stability and durability. In contrast, smaller displays, such as those in smartphones and tablets, benefit from thinner glass, enhancing portability and aesthetic appeal.
Impact of Display Resolution and Quality
As display resolutions increase, the demand for finer control over pixelation grows. Higher resolution displays often require thinner glass to accurately control the alignment of liquid crystals at a micro level. This is crucial for achieving the sharp, clear images expected in high-definition displays.
Balancing Durability with Precision
The thickness of LCD glass also reflects a balance between durability and precision. Thicker glass offers better protection against physical stress and damage, making it suitable for industrial displays or devices used in harsh environments. Conversely, thinner glass provides better control over the liquid crystal layer, essential for high-quality image display in consumer electronics.
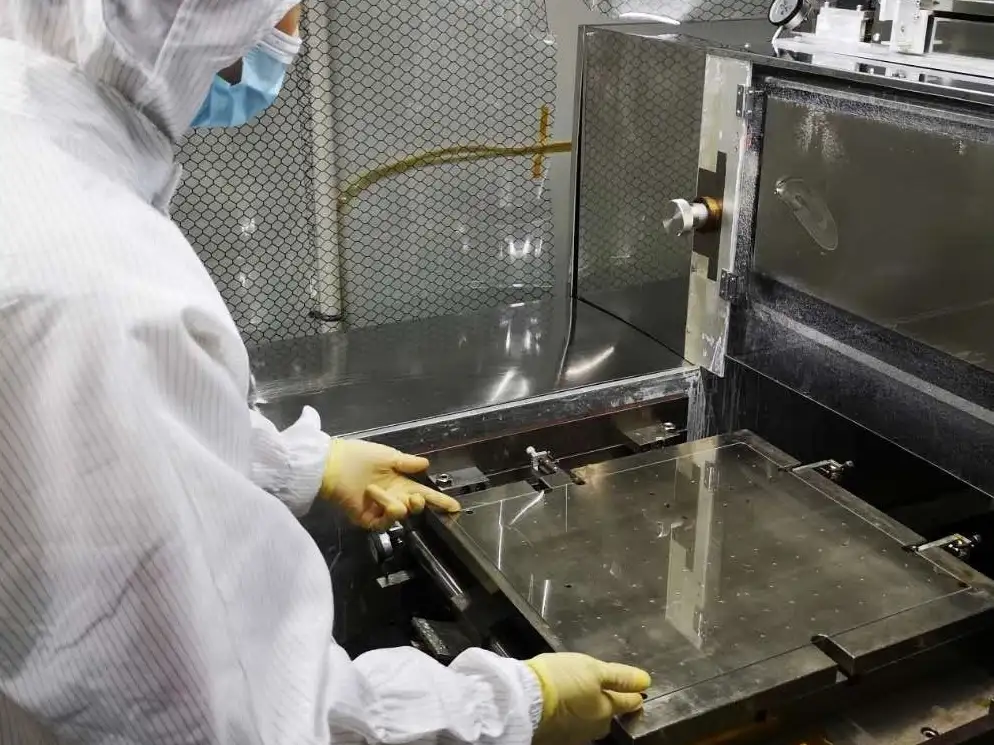
Manufacturing Considerations
The manufacturing process and cost implications also influence the thickness of LCD glass. Thicker glass may increase the overall cost of the display due to more material usage and potentially more complex manufacturing processes. Manufacturers must consider these factors alongside consumer demand and technological capabilities to determine the optimal thickness for their LCD glass.
Typical Thickness Range
The thickness of LCD glass can vary widely based on the specific requirements of the display. Generally, the thickness ranges from about 0.3mm to 3mm. This range encompasses a variety of display types and applications, each with its unique demands.

Thickness in Different LCD Types
- TN/STN/FSTN LCDs: These displays, often used in simple, low-power devices like calculators and digital watches, typically have a glass thickness ranging from 0.3 to 1 mm. Their simple design and low-resolution requirements allow for thinner glass.
- COG (Chip-On-Glass) LCDs: COG technology, where the electronic driving circuits are directly mounted on the glass, usually requires a thickness between 0.5 to 1.5 mm. This range ensures enough support for the circuitry while maintaining a slim profile.
- VA (Vertical Alignment) LCDs: Known for their high contrast ratios and wide viewing angles, VA displays usually have a glass thickness of about 0.7 to 1.2 mm. This thickness supports the advanced technology used in VA panels.
- TFT (Thin Film Transistor) LCDs: Common in computer monitors and TVs, TFT LCDs typically have a glass thickness in the range of 0.5 to 2 mm. The need for better color reproduction and faster response times in these displays often requires thicker glass.
- OLED Displays: OLED technology, which does not require a backlight, allows for even thinner glass, often less than 0.5 mm. This makes OLEDs ideal for lightweight and flexible applications.
Technological Advancements and Thickness
Towards Slimmer and Stronger LCD Glass
The quest for thinner LCD glass without compromising strength and durability has been a significant driver in the evolution of display technologies. This journey is marked by continuous innovation, both in the materials used and the manufacturing processes applied.
Pioneering Materials
Advancements in material science have played a crucial role. The development of chemically strengthened glass, for instance, has been a game-changer. This glass undergoes a chemical process that replaces the sodium ions in the glass surface with larger potassium ions, creating a layer of compressive stress. This process significantly enhances the strength of the glass, allowing it to be thinner while retaining, or even improving, its durability.
Enhanced Manufacturing Techniques
Manufacturing processes have also evolved to enable thinner glass production. Precision in manufacturing has reached a level where even the slightest variations in thickness are meticulously controlled. This precision ensures uniformity in the displays, which is crucial for maintaining image quality, especially in high-resolution screens.
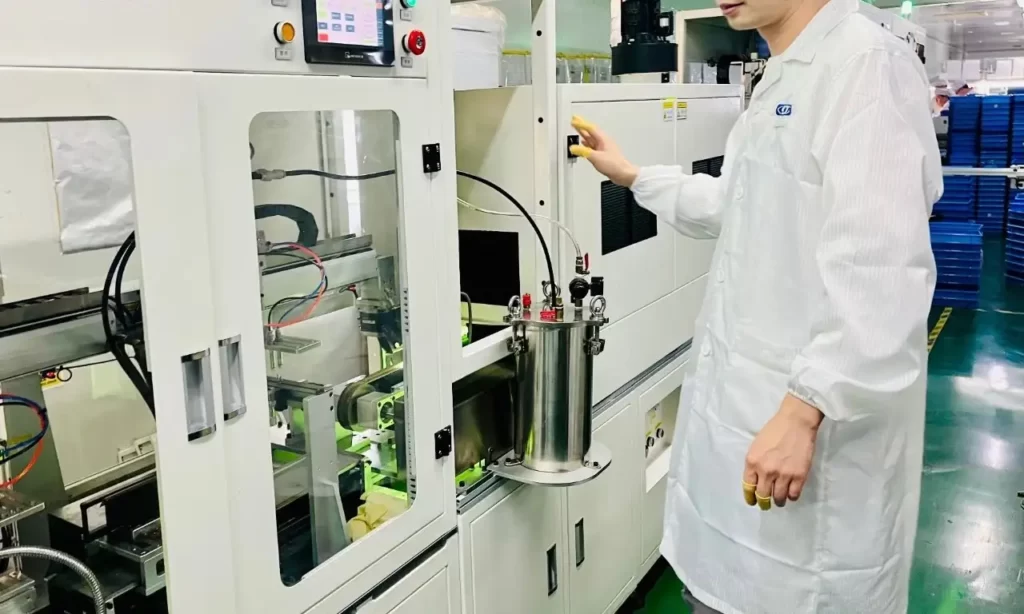
Layer Reduction Strategies
Another notable advancement is the reduction of layers within the LCD assembly. Earlier LCDs required multiple layers – including separate layers for touch capabilities, color filters, and light diffusion. Modern techniques have enabled the integration of these functionalities into fewer layers, thereby reducing the overall thickness.
Balancing Thinness with Functionality
The Challenge of Thinness
As LCD glass gets thinner, new challenges emerge. Thinner glass is more susceptible to damage from bending and impact, which can be particularly concerning in portable devices like smartphones and tablets. The industry’s response has been to innovate not just in terms of materials but also in how these materials are used within the device’s overall design.
Reinforcement Techniques
Manufacturers have employed various reinforcement techniques to bolster the strength of thin glass. These include framing methods where the glass is supported by a robust frame that absorbs impact and reduces the stress on the glass itself. Additionally, advancements in adhesive technologies have led to stronger bonding between the glass and the underlying display components, adding to the overall structural integrity.
Future Directions
Thinner Yet Stronger
The pursuit of even thinner and stronger LCD glass continues. Research is ongoing in developing new glass compositions and strengthening techniques. There’s a growing interest in materials like Gorilla Glass and Dragontrail, known for their exceptional strength-to-thickness ratios.
Sustainability Considerations
With an increasing focus on sustainability, future advancements will likely also consider the environmental impact of LCD glass production. This includes reducing the energy consumption in manufacturing processes and exploring recyclable or more environmentally friendly materials.
The Role of Nanotechnology
Nanotechnology holds promising potential in the development of future LCD glass. By manipulating materials at the molecular or atomic level, it might be possible to create glass that is not only thinner and stronger but also possesses additional functionalities like self-cleaning surfaces or improved touch responsiveness.
Learn more about Is LCD a Glass or Plastic?
Industry Standards
Setting the Benchmark
There are industry standards and norms that guide the manufacturing of LCD glass, ensuring consistency and quality across products. These standards often dictate the minimum and maximum thickness for different types of displays, considering factors like usage, resolution, and size.
Learn more about Why is Proper Cleaning Essential for LCD Glass?
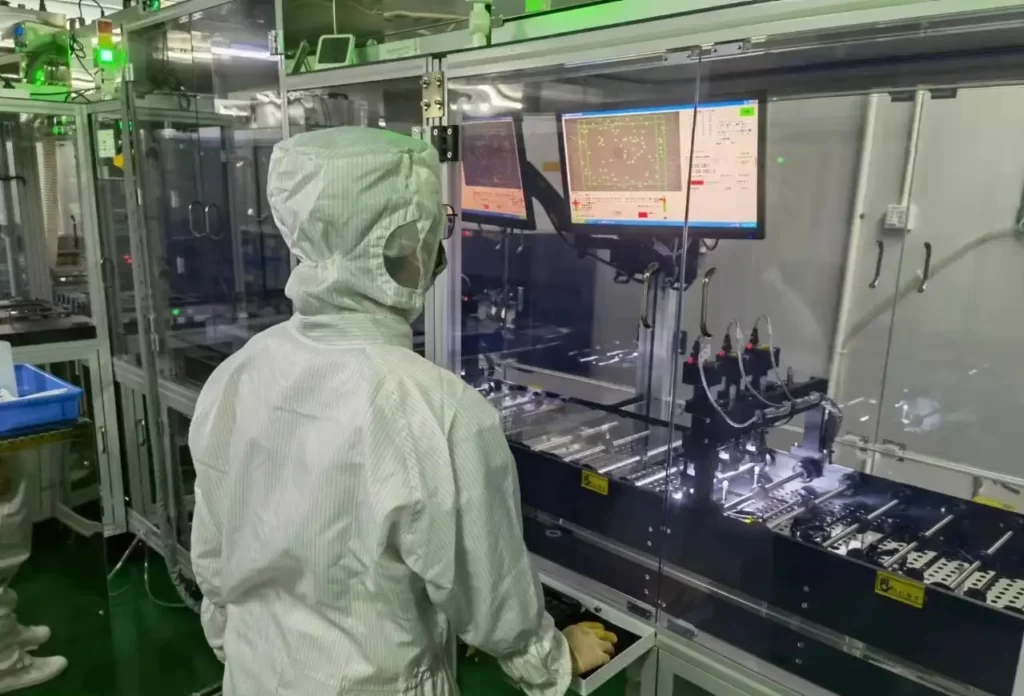
Compliance and Quality Assurance
Manufacturers like Longtech Optics Co. Ltd adhere to these standards rigorously. This adherence is not just about meeting regulatory requirements; it’s also about ensuring that every product delivers the performance and durability expected by the end-users.
Conclusion
In conclusion, the thickness of LCD glass is a critical factor that influences the design, performance, and application of LCD displays. From enhancing image quality to ensuring durability, the role of LCD glass thickness cannot be overstated. At Longtech Optics Co. Ltd, our commitment to excellence is reflected in our adherence to industry standards and our continuous innovation in the field of industrial LCD displays. Understanding the nuances of LCD glass thickness helps us in designing and manufacturing products that not only meet but exceed the expectations of our diverse clientele.